The relationship between Industry 4.0 technology and zero harm
Blog

Of the ‘zero’ goals that miners are striving towards, zero harm is the most emotive.
In the developed world, fatality and injury rates have trended downwards year-on-year for decades, however in the past 20 years or so, improvement has somewhat plateaued.
In 2020, there were 29 mining-related fatalities in the US (down one from 2019 and following rises in 2017 and 2018*) and in Australia, five people lost their lives in 2020 (down from 9 in 2019, but six have died during 2021 to-date†). Whilst such low numbers could be considered a success, it’s not enough.

Existing Industry 1.0 to 3.0 technologies have played a huge role in the massive improvements we’ve seen in the past century, (as has miners’ focus on safety, improvements in mine design and construction, as well as enforced regulatory minimums), however it’s very unlikely that they will be able to take us any further - additional improvement without change will be very hard to come by.
Industry 4.0 technologies and custom built sustainability solutions present the mining sector - arguably for the very first time - with the opportunity to actually reach zero harm; an objective that most of the world’s largest miners have committed to strive for‡.
From taking people out of harm's way, enabling real-time monitoring and threat mitigation, through to AI-led interventions that can predict and remedy danger before it even occurs; the mining sector now has at its disposal the tools to make mining as safe as office work -in fact, in some instances, by making it just that.
Industry 4.0 = Zero Harm
Mines are the embodiment of a hazardous working environment. With humans interacting with dangerous machinery and plant, hazardous and toxic materials, electricity, explosives, cliff edges, underground tunnels and much more; the sheer number of ways that someone in that environment can come to harm is extensive.
The mining sector has been very good at putting in place safeguards, processes, policies, and procedures that have taken harm measures to where they are today. Health, Safety and Risk assessments, training and other human elements have never been more comprehensive, although adherence and reporting can always be a challenge.
The US’s Mine Safety and Health Administration (MSHA) has multiple mining accident classifications* and there’s even more that the mining sector needs to consider beyond mineral extraction.
Each of these comes with its own set of individual technologies that can be applied to prevent or protect from each individual type of incident. Better PPE, safer Plant, improved mine design etc. will always play a role however the true path to zero harm can be lost in this detail.
The answer is Industry 4.0 technology that is capable of monitoring and analysing mining operations in real-time, predicting potential problems and triggering action, shutdowns or guiding improvements (e.g. an individual that’s risk taking) to stop impending harm.
The path to zero harm, Industry 4.0, and the need for extreme interoperability.
The fourth industrial revolution - where businesses build upon their use of computing power and automation with the adoption of intelligent, autonomous systems that can leverage complex data sets and machine learning to deliver AI-driven enhancements in real-time - is the missing piece in zero harm goal attainment.
There are a vast number of opportunities for miners to transform in the context of health and safety, both operationally and strategically via the adoption of new forms of IT, Mining Technical solutions (MT), Physical Technology (PT) and Operational Technology (OT) into existing operations. However, zero harm (and true Industry 4.0 transformation) will be achieved by finding better ways of doing things, the enhanced usage of data, and improving how people interact with it and a mine’s operations -not the technology itself.
Achieving zero harm is a significant endeavour, only made more complicated by the complexity of mining operations, systems and technologies - it can’t be achieved overnight by plugging in a single piece of technology that makes you Industry 4.0 and switching it on.
No, the path to achieving Industry 4.0 status is via the adoption of a suite of use case-specific sustainability solutions that can be deployed and then integrated with one another piece-by-piece, function-by-function.
Each of these solutions will improve singular (or more) aspects of your operations’ health & safety (or other parts of your operations that’s interrelated, such as environmental monitoring), but will then also need to connect to something that’s capable of a supremely high-level of interoperability, which can analyze all of the data that’s coming from these solutions (plus other systems or data sources inside and outside your organization) to identify trends, relationships and insights hidden in the ‘Big Data’ you’re accumulating. The platform also needs to be capable of taking direct action to prevent harm or identify where and how a business (or individual employee) needs to improve, optimizing on an ongoing basis based on changing variables and performance - it’s not about analyzing all the data; it’s about identifying the pertinent data to safety in this maelstrom, monitoring it accurately in real-time, and then using predictive analytics to stop harm from occurring or find safer ways of operating.
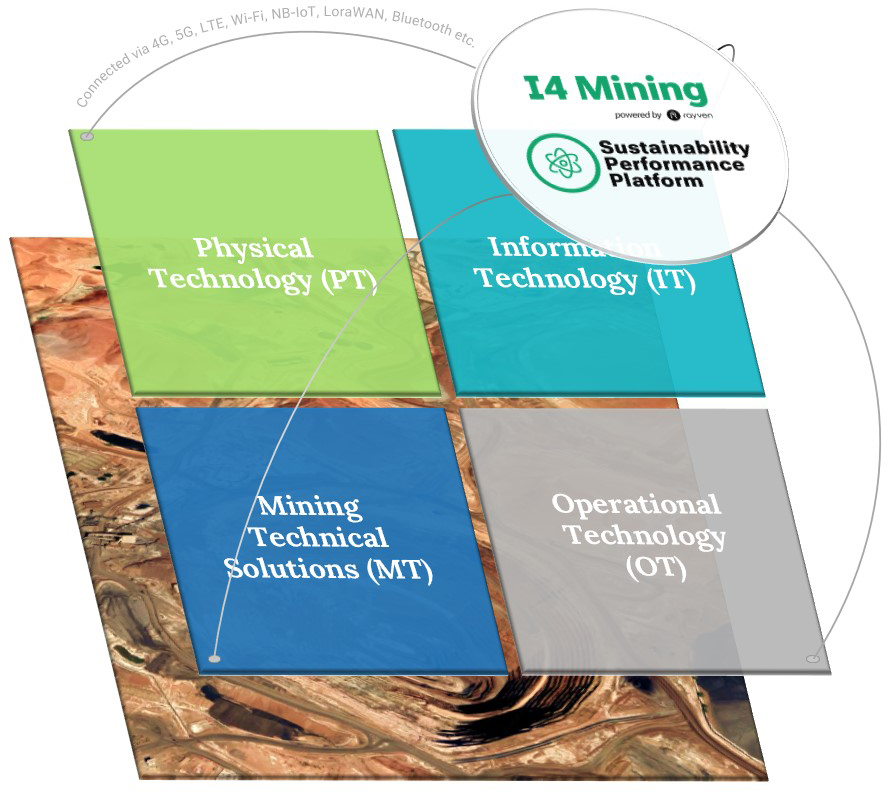
What is being described here is the technology platform that all of our sustainability solutions are built on, a new piece of technology that’s needed to sit in the middle of every Industry 4.0 business and/or operation to analyze and orchestrate: a Sustainability Performance Platform (SPP).
The Sustainability Performance Platform (SPP) is critical because it’s the one place in an organization where all of its data (both historical and real-time, from any system, sensors or data lake) can flow and be standardized for analysis, where machine learning algorithms can be leveraged, and where cross-functional decisions -made by human or AI -can be orchestrated and executed: it’s an Industry 4.0 organization’s brain.
I4 Mining is a sustainability technology provider to the mining sector, offering ready-to-deploy ESG solutions that help miners to succeed both strategically and operationally without ever getting in the way of good business.
Our solutions enable you to easily develop strategies, deliver accurate sustainability metrics and reports in real-time, improve sustainability and business performance, as well as make predictive analytics and forecasts part of your everyday so that you can reduce risks and optimise from mine-to-market.
Speak to us today to book a demo and discover how you can get started on your digital sustainability journey.
* Source: https://www.amsj.com.au/29-mine-related-deaths-in-us-in-2020/
† Source: https://www.safeworkaustralia.gov.au/statistics-and-research/statistics/fatalities/fatality-statistics up to 14-Oct-21
‡ Source: Principle 5 of the ICMM Mining Principles charter - https://www.icmm.com/mining-principles/5
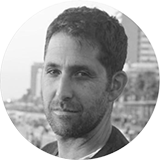
Jared Oken
CEO @ Rayven
jared@rayven.io
LinkedIn
Want to know about industrial AI + IoT more broadly?
If you'd like to find out more about the technology that underpins all of our digital mining solutions, other industrial uses of AI + IoT, or are eager to get into the detail of precisely what AI and IoT technology are then visit the Rayven blog.