Plant + Industry 4.0: the applications: Part 1
Blog

There are a huge array of technologies and solutions that can be applied to plant that can assist the mining sector in achieving their strategic goals.
Business are hugely reliant on their plant to dig, move, drill, spray, crush or build. With so many uses, fleets can be large, diverse and geographically spread; making them incredibly difficult to not only monitor and manage but get the most from them.
Reducing total cost of ownership, servicing and changing parts only when needed, increasing uptime, and learning what models and makes of plant provide the longest lifespan can have a huge impact on an organization's bottom-line. To achieve these goals (and a lot more), sustainability solutions can have a massive and immediate impact.
Rather than focusing on particular technologies (such as the electrification of assets and the increasing use of driverless technologies), we think it important to focus on the array of strategic impacts that the application sustainability solutions built on a Sustainability Performance Platform (SPP) – with access to the right data – can have on the business rather than the functionality that it provides i.e. it’s important not to put the cart before the horses.
Industry 4.0 sustainability solution plant Applications:
Real-time plant monitoring + utilization metrics. Some plant is autonomous, but the vast array isn’t. Simple real-time monitoring IoT technologies can enable its location to be tracked and individual functions measured second-by-seconds (such as vibration, noise, temperature, energy usage, flow, pressure, operator control application etc.) which, coupled with live production data, can provide a real-time view of how plant is performing and it’s live utilization metric from anywhere, at anytime. In the field this could provide a productivity score or on the production floor, a real-time OEE measure. It also unlocks the potential for many other benefits, such as: geo fencing and theft detection, better plant allocation, reduced energy consumption, operator safety scoring, lowered insurance costs, proximity real-time alerts, compliance guidance, remote tracking, asset class comparisons, pinpoint underutilized machinery, improve maintenance regimes and much more. Verizon found that, on average, fleet tracking technology repays its ROI in less than one year*.
Time to failure + predictive maintenance. There are many things that go into the failure of plant. Poor operation, difficult terrains, as well as the failure of individual parts. By using the data coming from real-time monitoring, historical and third-party data sources (such as weather, forthcoming usage and operator schedules), and the application of machine learning algorithms, it is possible to predict when plant is going to fail and why, as well as what the remedy is. This not only makes it possible to predict when machinery needs to be serviced (versus when it’s scheduled to be, simply because it’s been 6 months since its last check), but also identifies what the fix is (reducing maintenance crews time in the field) and prevents the development of problems that could cause hazardous failures that do harm to personnel and production. Benefits include: increased utilization, decreased scheduled downtime, reduced maintenance costs, prevent catastrophic failures and breakdowns, enhanced safety and compliance, increased asset lifespan, lower spare part inventory costs, quicker fixes, and more. McKinsey have demonstrated a 20% reduction in downtime and production increases† and PwC found it can reduce maintenance spend by 14%‡.
Performance analysis + real-time production optimization. A sustainability solutions built on a Sustainability Performance Platform (SPP) makes it possible to analyze data sets across fleets, utilizing all the data from every system internal or external, to identify and predict plant performance. With the use of real-time data measurements, automation and staff alerts, it’s possible for the platform to optimize performance and improve uptime and production immediately, meaning that plant can run optimally at all times, thereby improving yields and efficiencies. Additionally, through identifying patterns (such as how long it takes for an asset to start or whether it does better at a certain time of day), it is possible to use these insights to enhance safety and productivity by changing shift patterns and ensuring the correct personnel are on-site at the right time, e.g. have more maintenance staff rostered when failures tend to occur, change shift switchover times, or have attendants by machinery on the processing floor during higher-risk periods.
Autonomous vehicles + plant enhancement. Autonomous vehicles have been operating in mines for some years now and in that time they’ve demonstrated fuel efficiency savings and kept workforces out of harm’s way, but there are numerous assets and plant that are yet to be transformed. Their growth is only going to grow as miners look to move people out of harm's way and find efficiencies. McKinsey estimates that by 2035 autonomous mining using data analysis and novel technologies like AI will save the mining sector between US$290bn-US$390bn annuallyΩ and further adoption of the technology (plus the growing data sets that come from) coupled with analysis via an integrated AI + IoT platform will offer new productivity, safety and efficiency benefits that enhance bottom-line results.
Establish operator performance + safety scores. Through the analysis of real-time plant data monitoring, wearables, third party sources and by comparing it with environmental measures and operational understanding, it’s possible to monitor employee performance based on the individual aspects of their role, as well as how safe they’re being. This enables miners to identify when, for example, an employee is tired or beginning to make small mistakes and could be about to come to harm, whether they’re consistently following required compliance standards, or if they’re performing much better than their peers. In one trial, by providing operators with direct feedback based on how they were driving their trucks, they were able to limit peak speed, reduce short stops and restarts, and avoid abrupt braking and strong acceleration. In just eight weeks, fuel consumption dropped by 7%*.
Standard operating procedure adherence + safety margins. Putting in place all of the safeguards and procedures needed to achieve zero harm is always going to be ineffective if incidents aren’t reported, standards aren’t followed or if the safety margins that they are based upon are insufficient. Through real-time monitoring of plant and employees, it’s possible to identify where deviations are occurring, where margins are insufficiently strict (or even where they’re too constraining), as well as pick up on the small incidents that may never make it onto incident reports but which, occurring repeatedly over time, may be a key lead indicator of a problem that could have potentially more catastrophic consequences.
Catastrophic failure prevention. The real-time monitoring of plant, even with the use of predictive machine learning algorithms, needs time and large data sets to be able to learn from past failures and anomalies to predict future ones. What can be achieved sooner (and more accurately), however, is the prediction of catastrophic failures. Increased heat, vibration, bending and noise invariably proceed a total failure – even if it’s just by seconds. Through the use of sustainability solutions built on a Sustainability Performance Platform (SPP) and real-time monitoring of data from the plant, it’s possible to identify impending failures and implement fail-safe machinery shutdowns by understanding operational norms, the outcome of previous breaches of them across fleets, and by being able to identify from real-time measures where recovery won’t be possible; utilizing automations to exert control and intervene. This not only prevents potentially hazardous situations where personnel or the environment come to harm, but catastrophic failures are generally bigger, more expensive and take much longer to repair.
See the 2nd part of this blog here for the other applications!
I4 Mining is a sustainability technology provider to the mining sector, offering ready-to-deploy ESG solutions that help miners to succeed both strategically and operationally without ever getting in the way of good business.
Our solutions enable you to easily develop strategies, deliver accurate sustainability metrics and reports in real-time, improve sustainability and business performance, as well as make predictive analytics and forecasts part of your everyday so that you can reduce risks and optimise from mine-to-market.
Speak to us today to book a demo and discover how you can get started on your digital sustainability journey.
* Source: Verizon Connect - 2021 Fleet Technology Trends Report
† Source: PwC - Mine 2021‡ Source: https://insight.thinkiq.com/blog/how-industry-4.0-smart-manufacturing-improves-mine-to-metal-efficiency-for-mineral-manufacturers
Ω Source: McKinsey: Beyond the Super cycle: How technology is reshaping resources
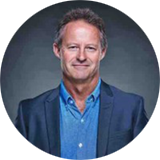
Phillip McBride
CSO & Technologist @ Rayven
phillip@rayven.io
LinkedIn
Want to know about industrial AI + IoT more broadly?
If you'd like to find out more about the technology that underpins all of our digital mining solutions, other industrial uses of AI + IoT, or are eager to get into the detail of precisely what AI and IoT technology are then visit the Rayven blog.