Mining ESG Industry 4.0 AI + IoT use cases: Part 1 - Enhancing operational performance.
Blog

This is the first in a series of three blogs examining the different applications of Industry 4.0 technology in solving the mining sector's SDG and ESG goals.
The modern approach to mining using best practices when it comes to ESG* involves:
a) The establishment of a pre-mining baseline from which to monitor environmental effects (and their impact on people) during mining and help establish geologically reasonable closure goals;
b) The identification of environmental risks related to mining through standardised approaches; and
c) The formulation of an environmental closure plan before the start of mining.
Whilst analysing Industry 4.0 use cases, it would be easy to segment and silo them into each stage, however that undermines the full-cycle role that the technology has.
Environmental harm can occur at any point from multiple sources, and whilst there may be a novel (or old) technology that can solve these individual occurrences, when talking about Industry 4.0 technology, what we’re really trying to do is provide new ways to analyze risk holistically (using machine learning) and then improve functions to achieve a strategic business objective (not a technology one) based on that analysis.
Therefore, to explore the application of Industry 4.0 technology in mining, it’s important to focus on operational areas where the application of sustainability solutions built on a Sustainability Performance Platform (SPP) can have significant impacts, rather than the analysis of a particular technology (such as drone usage or driverless technologies).
Enhanced operational performance:
Production improvements. The use of sustainability solutions built on a Sustainability Performance Platform (SPP) in the manufacturing sector has been widespread and many of the optimizations and efficiencies that it provides can be directly adopted by the mining sector during refinement, processing and production. From finding energy efficiencies, improving yields, OEE optimization, all the way through to predictive maintenance and downtime prevention, the technology can help miners to increase efficiencies and adopt optimal processes that reduce waste and the environmental impact of activities.
Reduce waste. Through the use of sustainability solutions built on a Sustainability Performance Platform (SPP) it’s possible to identify where further resources can be extracted from waste materials, reducing environmental impact and improving productivity. For example, it can direct miners to tailings where valuable resources exist in quantities that make it cost-effective to extract or identify where in situ leaching or recovery (ISL / ISR) opportunities exist.
Recycling. The circular economy is a growing narrative and the mining sector, like many others, can take advantage of it -fuelled by Industry 4.0 technology. From using advanced analytics to review and revisit waste material from historical operations with a view to reprocessing them with modern techniques, identifying what removed material can be used safely for construction and other purposes, and working with the wider value chain, in particular with metal reprocessing facilities, mining companies can find more value with minimal additional inputs and reduce waste.
Better waste management. Mining creates a lot of spill, tailings and other waste which, if improperly handled, can have serious environmental impacts. Industry 4.0 technology can enable miners to monitor how it is being handled in real-time, scrutinizing process adherence, plant and personnel performance, and ensuring that the tonnage of waste expected arrives where it should (reconciliation), whether it’s being treated/incinerated/stored properly, and assess whether there are potentially alternative ways of utilizing by-products to reduce waste.
Immediate, automated mitigation + remediation. Sustainability solutions built on a Sustainability Performance Platform (SPP) that utilize real-time data can provide miners with rapid, effective direction (as well as automated interventions) should the worst occur and an unexpected environmental event happen (or be about to). Learning from modelling and previous learned performance, the platform can leverage situational data and find better ways to mitigate unwanted outcomes, as well as monitor critical environmental measures in real-time to prevent breaches and harm from occurring via manual or AI-led automated interventions.
Manage shared infrastructure. One way of reducing costs associated with mining and investing in the community is to leverage shared infrastructure. Sustainability solutions built on a Sustainability Performance Platform (SPP) make this possible at a practical level, allowing for the better scheduling of usage, monitoring of maintenance needs, as well as uncovering the most efficient (and effective) way of running it. In some places, it will be possible for the renewable energy infrastructure created to supply a mine with electricity to feed into the local grid and/or subsidize the local community's energy usage, for example.
Resource discovery. The use of drones to better map topographical (as well as underground) sites, leveraging of third party data, as well as in-field sensors and collected geological data; make it possible to leverage a sustainability solution built on a Sustainability Performance Platform (SPP) to identify where on a site the best (and most profitable) material is, explore the different ways of extracting it, and predict the potential environmental impacts of each of them to find the best, most long-term cost-effective locations and methods of extraction.
Energy efficiency. Ventilation represents a huge cost in underground mines, but are critical in ensuring a safe working environment by removing fumes, gases and smoke, as well as in controlling temperature. A sustainability solution built on a Sustainability Performance Platform (SPP) can be used to forecast peaks, automatically adjust ventilation systems and find improved operational schedules. The result is that systems don’t necessarily need to run around-the-clock everywhere and can save up to 40% of energy costs†.
Plant electrification + hydrogen fuel cells. The benefits of electrifying assets or moving to Hydrogen technology have been widely discussed. Whilst not a panacea to achieving ESG initiatives, it will go a long way in reducing carbon and other harmful gas emissions, creating safer working environments and adding to efficiencies -as long asthe power that’s being used to drive it is from renewable or zero carbon sources. Goldcorp’s Borden mine in Ontario, Canada has been completely electrified. This demands a 25-30% premium on the cost of equipment (although this will reduce in time), but the savings over the long term are significant with Goldcorp expecting to save CA$9m annually in operational costs from lower diesel use as well as a 70% reduction in greenhouse gas emissions.
Autonomous plant + automation. Autonomous vehicles have been operating in mines for many years and have demonstrated fuel and efficiency savings, kept people out of harm’s way, and made a positive impact on measurable ESG goals. There are numerous assets and plant that are yet to be transformed, as well as new use cases to be explored, such as with predictive maintenance. At Vale’s Brucutusite in Brazil, the company estimates that automation is increasing plant lifespan by 15%, whilst fuel and maintenance costs are decreasing by 10%Ω. The growth of the technology, coupled with sustainability solutions built on a Sustainability Performance Platform (SPP) will enable new optimal processes to be modelled and implemented –in real-time –as well as provide predictive insights that will offer new productivity, safety and efficiency benefits that enhance bottom-line results and environmental measures.
Optimal plant configuration. A sustainability solution built on a Sustainability Performance Platform (SPP) can be leveraged to provide real-time, ongoing plant optimization based on real-time data being collected from it and the wider environment. For example, should a piece of machinery be expelling excessive amounts of fumes or vibrating too much, configurations can be adjusted to run the machinery more efficiently, resulting in reduced risk of a failure, environmental harm, and improving efficiency.
Real-time catastrophic failure prevention. Real-time monitoring of assets and plant, even with the use of predictive machine learning algorithms, need time and large data sets to be able to predict things 100% accurately (and it’s arguable whether it can go beyond 99.9%). Therefore, using sustainability solutions built on a Sustainability Performance Platform (SPP), it’s possible to analyze the real-time data measures and implement fail-safe plant shutdowns should a catastrophic failure be impending by understanding operational norms, the outcome of previous breaches of them, and by being able to identify from real-time measures where recovery won’t be possible; directing machinery to shut down immediately via automated intervention. This can stop major environmental (and safety) events before they happen.
See the 2nd part of this blog here for Real-time personnel, environment & plant monitoring use cases.
See the 3rd part of this blog here for Holistic operational analysis use cases.
I4 Mining is a sustainability technology provider to the mining sector, offering ready-to-deploy ESG solutions that help miners to succeed both strategically and operationally without ever getting in the way of good business.
Our solutions enable you to easily develop strategies, deliver accurate sustainability metrics and reports in real-time, improve sustainability and business performance, as well as make predictive analytics and forecasts part of your everyday so that you can reduce risks and optimise from mine-to-market.
Speak to us today to book a demo and discover how you can get started on your digital sustainability journey.
*Source: Environmental Considerations Related to Mining of Nonfuel Minerals, US Department of the Interior and the US Geological Survey, 2017.
† Source: Natural Resources Canada, 2016 via the OECD’s ‘Mining and Green Growth’ report.
Ω Source: McKinsey: Beyond the Super cycle: How technology is reshaping resources
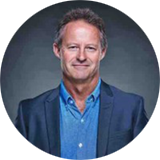
Phillip McBride
CSO & Technologist @ Rayven
phillip@rayven.io
LinkedIn
Want to know about industrial AI + IoT more broadly?
If you'd like to find out more about the technology that underpins all of our digital mining solutions, other industrial uses of AI + IoT, or are eager to get into the detail of precisely what AI and IoT technology are then visit the Rayven blog.