Mining ESG Industry 4.0 use cases: Part 2 -
Real-time personnel, environment & plant monitoring.
Blog

This is the second in a series of three blogs examining the different applications of Industry 4.0 technology in solving the mining sector's SDG and ESG goals.
In this blog, we look at the ways that Industry 4.0 technology and purpose-built sustainability solutions can provide miners with enhanced real-time insights that enable better decisions to be taken, faster - plus much more.
Real-time employee, environment & plant monitoring:
Real-time environmental monitoring. Perhaps the most obvious use of the technology, a sustainability solution built on a Sustainability Performance Platform (SPP) enables you to unite real-time data feeds from sensors on-site, with internal systems and third-party data sources to provide miners with accurate, real-time environmental measures that enable them to more accurately gauge baseline values prior to opening a site, as well as during operation and post-closure. Leveraging the data, the solution can additionally provide predictive insights based on current operational models so that miners can judge future environmental performance. It also unlocks the potential for many other benefits, such as: fault and leak detection, geo fencing, reduced energy consumption, operator environmental and safety scoring, proximity real-time alerts, compliance guidance, remote tracking, plant class comparisons, pinpoint environmental areas of concern, improve maintenance regimes, and much more.
Better conversations with community + regulators. With real-time environmental monitoring in place, it’s possible to have better conversations with the people that are or will be impacted by operations. From providing real-time data feeds that demonstrate conservatorship through to accurately forecasting impacts and how post-closure remediation efforts are performing, conversations with community and regulators can be realigned and occur around actual current data and the accurate forecasts being provided from the AI + IoT platform.
Accurately monitor + measure entire global mining supply chain. A solutions built on a Sustainability Performance Platform (SPP) enables miners to get a complete, holistic view of their entire global supply chain in real-time. Via extreme interoperability, the platform can leverage any data source, no matter where it sits. This means that real-time data feeds from the wider supply chain can be leveraged, including real-time data from assets retrofitted with cheap IoT sensors, to provide miners with complete visibility of their supply chain and environmental performance.
Time to failure + predictive maintenance. There are many things that go into the failure of plant, machinery and equipment, but the environmental (and safety) impact of them can be severe. Poor operation, different terrains, as well as the failure of individual parts all have a role to play. With real-time monitoring of plant and the use of predictive algorithms that can utilize data from multiple sources, such as real-time temperature and vibration measurements coupled with forthcoming usage and operator schedules, it’s possible to predict when an asset is going to fail, why and what the remedy is. This not only makes it possible to predict when plant needs to be serviced (versus when it’s scheduled to be, simply because it’s been 6 months since its last check), but also identifies what the fix is (reducing maintenance crews time in the field) and prevents the development of problems that could cause hazardous failures. This means fewer interventions, greater efficiencies and a lower environmental impact.
Standard operating procedure adherence + safety margins. Putting in place all of the safeguards and procedures needed to achieve zero harm is always going to be ineffective if incidents aren’t reported, standards aren’t followed or if the safety margins that they are based upon are insufficient. Through real-time monitoring of operations, including plant and people, it’s possible to identify where deviations are occurring, where margins are insufficiently strict (or even where they’re too constraining), as well as pick up on the small incidents that may never make it onto incident reports but which, occurring repeatedly over time, may be a key lead indicator of a problem that could have potentially more catastrophic consequences.
Deliver proximity alerts + real-time Permit To Work. Many injuries and environmental harm occurs on site due to people being in the wrong place at the wrong time, doing something that they shouldn’t be, or through an unforeseen failure resulting in an action, such as inundation, gas explosion or rock fall. A sustainability solutions built on a Sustainability Performance Platform (SPP) enables miners to, via the use of wearables and the real-time monitoring of environmental and mine conditions, aggregate data in real-time and identify when something is going to occur, sending alerts to personnel or automatically stopping plant.
Inventory & waste monitoring + reconciliation. Mining uses many potentially harmful chemicals (some of which are controlled) and creates hazardous waste which, if released or stored in the incorrect circumstances, can cause huge amounts of environmental harm. A sustainability solution built on a Sustainability Performance Platform (SPP) enables miners to accurately track their usage, how it is being handled across supply chains, monitor storage conditions, and reconcile its use across sites.
Water treatment monitoring. Large amounts of water is utilized at different points of the mining lifecycle, as well as with certain extraction techniques. Modern mines process and treat water on-site before reusing it and/or discharging it into the environment. Through the use of a sustainability solution built on a Sustainability Performance Platform (SPP) you can monitor performance in real-time, identify process optimizations, and identify where further treatment may be necessary before discharge, avoiding harm.
Fill data gaps in ecological + hydrological knowledge. Much of the impact that mining may have on the environment isn’t definitively known. What’s more, different geologies, topographies, fauna, flora, weather patterns etc. all have a unique impact on a particular operation. Through the use of Industry 4.0 technology and a Sustainability Performance Platform (SPP), it is possible to measure much more accurately data from in-field sensors, business systems, as well as third party data to establish new, accurate measures which will enable miners to better predict the impact of operations, measure operations in real-time, and then monitor the effect of remediation efforts long after closure. An example of this in action is with Glencore’s drone usage to monitor NO2 fumes from blasting In real-time; not only are they learning more about the dynamic nature of blasts so that they can predict future outcomes from further activity, but it has removed much of the uncertainty around NO2 creation which was previously based on visual inspection of blast footage*.
Establish real-time employee safety + environmental scores. Through the analysis of real-time data monitoring via wearables, comparing it with environmental measures and operational understanding, it’s possible to monitor employee performance based on the individual aspects of their role, such as how safe they’re being. This could help identify when, for example, an employee is tired or beginning to make small mistakes and could be about to come to harm, whether they’re consistently following required compliance norms at any given moment, or if they have a ‘heavy foot’ and are using more energy than other operators. In one trial, by providing operators with direct feedback based on how they were driving their trucks, they were able to limit peak speed, reduce short stops and restarts, and avoid abrupt braking and strong acceleration -in just eight weeks, fuel consumption dropped by 7%†.
Enhanced safety walks + environmental inspections. The real-time, remote monitoring of environmental and mine measures is a more accurate, safer way of conducting critical safety and environmental procedures. Taking this a step further, you can use machine learning to predict how these variables are affected by third party data (such as weather) or your operations, providing you with real-time analysis that identifies problems in the afternoon that weren’t there in the morning, or that can predict the development of risks.
See the 1st part of this blog here for Enhancing operational performance use cases.
See the 3rd part of this blog here for Holistic operational analysis use cases.
I4 Mining is a sustainability technology provider to the mining sector, offering ready-to-deploy ESG solutions that help miners to succeed both strategically and operationally without ever getting in the way of good business.
Our solutions enable you to easily develop strategies, deliver accurate sustainability metrics and reports in real-time, improve sustainability and business performance, as well as make predictive analytics and forecasts part of your everyday so that you can reduce risks and optimise from mine-to-market.
Speak to us today to book a demo and discover how you can get started on your digital sustainability journey.
* Source: Safe to Work Magazine, https://safetowork.com.au/glencore-receives-recognition-for-safety-and-environment-initiatives.
† Source: BCG: Mining Value in AU, 2017.
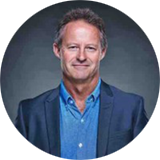
Phillip McBride
CSO & Technologist @ Rayven
phillip@rayven.io
LinkedIn
Want to know about industrial AI + IoT more broadly?
If you'd like to find out more about the technology that underpins all of our digital mining solutions, other industrial uses of AI + IoT, or are eager to get into the detail of precisely what AI and IoT technology are then visit the Rayven blog.