Why electrification won't be enough to achieve 'zero' goals
Blog

Electrification has an important role to play in achieving zero goals, but it needs quite a bit more.
The electrification of plant is going to have a huge impact on the mining sector. From reducing carbon, creating safer working environments and adding to efficiencies; its future role in Industry 4.0 transformation is all but ensured.
A boon for OEMs and supporting services, electrification will reduce operational costs and CAPEX because it reduces other infrastructure needs, such as ventilation shafts in underground mines to extract harmful diesel particulates. However, it’s important not to think of electrification as a panacea - it is a single technology that cannot alone drive transformation and achieve strategic ‘zero’ and profitability goals.
Where it will play a massive role is with data streams. By virtue of the way that electric plant is engineered (and increasingly so), it will be able to provide real-time performance insights like never before. However the complete changeover of every piece of plant in an operation will not occur overnight.
AI technology advances, old fleets and the need to electrify assets means that many operations, processes, and approaches must be overhauled using a mix of new plant and the retrofitting of others to ensure that plant’s natural, scheduled lifespan is seen-out (protecting past investments and profitability). This is where in-field real-time sensors and the use of IoT solution providers will help, by bridging the data gap when it comes to current assets’ use (or limited green electricity availability) up to the plant’s natural end of life and its replacement with electric alternatives (electricity grid-willing).
Where to from here? AI + IoT.
To deliver on the promises of electrification across operations, AI + IoT technology is needed.
Electrification delivers additional functionality that’s needed to either deliver on Industry 4.0 transformation or which can deliver on changes that have been identified by it. For example, systems that measure whether a seatbelt is plugged in or that allows for a drill rig to be run remotely is great in improving safety, but is not going to analyze whether the person at the controls is doing a good job or whether that particular piece of plant is performing as well as others in its class.
What else is needed a Sustainability Performance Platform (SPP).
A Sustainability Performance Platform (SPP) sits in the middle of your technology and operations. It integrates with all your other systems, platforms and data stores, offering extreme interoperability and creating a single source of truth through which you can analyze data, apply machine learning, seize optimizations either manually or via AI-led control, and much more (read more about this here).
With this platform in place, you can utilise or build sustainability solutions that use the data streams that come from your plant and combine them with other data feeds to provide you with significant safety, productivity and predictive analytics - all in real-time; i.e. you can apply this data to achieving real business goals and objectives.
Electrification + AI + IoT = Predictive Maintenance
A common goal within the mining sector is to improve maintenance regimes to seize on multiple improvements in multiple fields.
Predictive maintenance and catastrophic failures prevention is, therefore, a common place for businesses to start with Industry 4.0 technologies and a good use of the data coming from newly electrified plant. Whilst improving asset performance is always likely to be of benefit by improving uptime (which directly relates to productivity), it’s also likely to be closely tied to zero harm and efficiency measures.
How to get started with Predictive Maintenance.
Our advice with Predictive Maintenance would be to pick a particular plant class at a single site and then identify all of the potential variables that would likely affect its maintenance needs; including plant, human, process, environmental, asset etc.
Once established, it is necessary to explore where the data gaps are. Is there certain data that cannot be collected at this stage? What will you get through electrifying it? Is real-time data readily accessible? What’s the internal skills gap when it comes to the necessary technology, implementation or data analysis and use of AI?
Cited results from implementing a predictive maintenance regime within the mining sector:
- McKinsey ‘Mining Productivity Index’ has stated that they’ve identified operating efficiency improvements amounting to 70% of output due to breakdowns and stalled production.
- PwC stated in ‘Balancing Uptime and Working Capital: Maintenance and Inventory Strategies in Mining’ that effective condition monitoring of critical equipment can reduce maintenance spend by 14%.
- I4 Mining’s solutions have lowered cost of maintenance on key plant by 9% and decreased unscheduled downtimes by 63%.
Critical to developing an Industry 4.0 footing are sustainability solutions built on a Sustainability Performance Platform (SPP), so this should be the starting point. Utilizing someone that has an understanding of mining operations and good cross-functional technology and data science expertise is going to be critical, as many providers are industry agnostic or lack the in-depth understanding of a sector to add value during solution development.
The next step would be to further explore the technology stack that is going to be needed and pre-existing sustainability solutions. Central to this will be the in-field devices needed to collect real-time information, the integrations with systems (both internal and external), as well as the networks and comms which will be needed to transmit data to the Sustainability Performance Platform (SPP) and then action the instructions that are directed as a result of its real-time analysis. What’s more, it’s also important to begin developing (or buying) the machine learning algorithms that are going to be used to improve predictive maintenance of this plant at this stage, as there will be multiple options.
Once the full technology stack is identified, it’s about the deployment, roll-out and internal communication/transition plan. Every site and piece of plant is unique, but there are commonalities across classes, mines and operations that can be applied to every situation and across projects.
The best approach is to start small and scale. Pick an easy-to-monitor use case without too many variables, where improvement can be clearly measured, and look to apply it to a single site. This enables the rapid deployment of technology (sometimes in weeks), reduces costs and risks, and provides a pilot program through which data is beginning to be collected (bigger data sets = faster optimizations and quicker success).
Once making a measurable impact, it’s time to scale across multiple sites to capture bigger data sets from across operations or different types of plant. By scaling only at this point, it will be possible to utilize the learnings from the pilot to find efficiencies and enhance the optimization loop almost instantly. What’s more, by working with a partner that can work over the longer-term and, critically, knows how to scale will reduce costs, speed-up the deployment process, and reduce further development cycles.
Work with someone who is a digital native, can explore your operations in relation to your business objectives, who understands the sector, knows the current technology, and has a global network of best-in-class partners who can provide you with the future-proofed, ready-to-deploy sustainability solutions: talk to I4 Mining.
I4 Mining is a sustainability technology provider to the mining sector, offering ready-to-deploy ESG solutions that help miners to succeed both strategically and operationally without ever getting in the way of good business.
Our solutions enable you to easily develop strategies, deliver accurate sustainability metrics and reports in real-time, improve sustainability and business performance, as well as make predictive analytics and forecasts part of your everyday so that you can reduce risks and optimise from mine-to-market.
Speak to us today to book a demo and discover how you can get started on your digital sustainability journey.
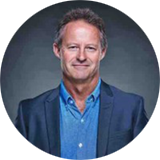
Phillip McBride
CSO & Technologist @ Rayven
phillip@rayven.io
LinkedIn
Want to know about industrial AI + IoT more broadly?
If you'd like to find out more about the technology that underpins all of our digital mining solutions, other industrial uses of AI + IoT, or are eager to get into the detail of precisely what AI and IoT technology are then visit the Rayven blog.